쉐퍼시스템즈의 낱개 별 - 단일 낱개 픽킹
인트라로지스틱스(intralogistics) 프로세스에 원활히 통합될 수 있는 완전자동화라는 개념을 사용한다면 합리적이고 신뢰할 수 있는 맞춤형 제품 취급을 목표로 이상적인 기반을 마련할 수 있습니다. 쉐퍼시스템즈는 이를 위해 로봇 지원 팔레타이징 및 픽킹을위한 맞춤 모듈식 솔루션과 물류센터 내 단일 피스 픽킹을 위한 고성능 로봇공학 애플리케이션을 제공합니다.
시장을보면 방향을 알 수 있습니다
직원 10,000명당 로봇 설치율을 보여주는 주요 척도인 로봇 밀도는 매년 증가하고 있습니다. 현재 직원 10,000명당 113기라는 로봇밀도는 현재 최고 수치입니다. 독일의 로봇밀도는 346기(로봇)로 세계 4위이자 유럽 내 선두이며, 스웨덴과 덴마크가 그 뒤를 쫓고 있습니다.[1] 현재 제조업 분야의 로봇 설치 비율이 가장 높지만 물류 시장이 그 뒤를 잇고 있습니다.
사실 이러한 변화는 인트라로지스틱스 프로세스에서도 점진적으로 이루어지고 있습니다. 디팔레타이징, 팔레타이징 또는 픽킹에 관계없이 고성능 로봇 기술은 많은 물류센터에서 없어서는 안 될 필수 요소가 되었으며 높은 성과율에 필수 동력입니다.
쉐퍼시스템즈의 픽킹 기술
쉐퍼시스템즈는 피스픽킹 및 케이스픽킹 솔루션을 제공합니다. 케이스픽킹은 보통 소매상에 매장 친화적인 팔레트로 공급하는 배송센터에서 활용됩니다. 활용 분야에 따라 모든 온도 범위(영하 28°C의 냉동 포함) 및 모든 성능속도에서 지능형 물체 인식과 함께 검증된 그립핑(gripping) 원리가 사용됩니다.
사용 빈도가 높은 또 다른 솔루션은 바로 피스픽킹입니다. 즉 낱개를 배송 빈(bin)에 넣는 것을 의미합니다. 피스픽킹은 가장 비용이 많이드는 프로세스 중 하나이며, 고효율 처리를 위해 특별한 주의가 필요합니다. 여기서 주의해야 할 두가지 사항으로는 안전하고 부드러운 제품취급과 지능형 소프트웨어 기술의 최적화 사용입니다.
스마트하고 유연한 피스픽킹
기계학습 러닝 및 특히 최적화된 초고성능 알고리즘은 픽킹로봇의 생산성을 위한 필수 요소입니다. 현재의 알고리즘을 사용하는 로봇은 인공 지능(AI) 및 3D 이미지 처리 덕분에 미리 정의된 동작 시퀀스를 보다 많이 반복할 수 있을 뿐만 아니라 더 복잡한 작업도 수행할 수 있습니다. 로봇들은 상황에 따라 대응하고 행동할 수 있으며, 이에 따라 더 복잡한 인트라로지스틱스 애플리케이션 시나리오에도 더욱 적합한 형태로 발전하고 있습니다. 인트라로지스틱스에서는 모든 개별 배송마다 고유의 특성이 있으며 개별 픽킹프로세스의 결과라 할 수 있습니다. 자동 및 반자동 솔루션은 효율성을 향상시킨다는 측면 이외에도 특히 건강에 해로운 반복적 활동에서 작업자들에게 인체공학적인 근무 환경을 제공하는데 집중합니다. 이런 솔루션 덕분에 개별 프로세스들이 서로 순조롭게 조화될 수 있습니다. 로봇은 성능, 견고성 및 품질 면에서 배송 품목의 범위가 적절히 설정되어 있고 적합한 자동화 환경에서 사용되는 경우, 수동 솔루션에 비해 몇 가지 이점이 있습니다. 이런 맥락에서 오늘날의 특수 알고리즘은 몇 년 전에는 상상도 할 수 없었던 것을 가능하게 하기 때문에 의미 있는 발전이 이루어졌습니다. 로봇은 원통형과 정육면체, 원뿔형 등 매우 다양한 형태의 물체를 집는 데 적합합니다.
성공요인으로서 통합자(Integrator)의 역량
표준화된 피스픽킹 로봇 애플리케이션은 다양한 주문구조에있어 요구조건을 충족시킬 뿐만 아니라 여러 산업부문에서도 활용될 수 있습니다. 쉐퍼시스템즈 피스픽킹 애플리케이션은 기존 시스템에 원활하게 통합될 수 있습니다. 활용 분야와 프로세스 환경에 따라 고성능 픽킹로봇은 시간당 최대 1,000회의 픽킹성능을 달성합니다.
모든 애플리케이션의 목표는 항상 동일합니다. 바로 최대 성과를 달성하는 것입니다. 물론 프로세스의 신뢰성이 최대한 보장되어야 합니다. 이 야심찬 목표를 향해 가는 길에 우리는 다음과 같은 성공 요소들을 중요하게 생각합니다. AI 비전(생산 및 물류에서의 이미지 인식)과 같은 피스픽킹 애플리케이션을 위한 통합자의 포괄적 역량, 검증된 스캔 기술, 쉐퍼시스템즈의 소프트웨어 WAMAS® Lighthouse로 실시간 시스템 시각화를 이용한 로봇 셀을 상세히 분석하기 등이 이에 해당됩니다. 마지막 세번째 요소를 통해 중요한 운영 데이터를 수집하여 필요한 유지보수 주기를 계산할 수 있습니다. 이 유지보수 예측 방법은 유지보수 시기를 예측 및 계산할 수 있게 하며 설비 가동 중단 현상을 방지하는 데 도움이 됩니다.
이에따른 결과에는 분명한 이점이 있습니다.
일정한 성능을 유지할 수 있는 시스템의 높은 가용성을 위한 스마트 로봇 솔루션
물류센터 관리 시스템인 WAMAS를 기존 인프라에 완벽하게 통합
피크 시간과 계절적 변동에 모두 대처 가능한 최적화된 그리핑 및 제품별 로봇 가속화를 통해 높은 프로세스 신뢰성으로 최대 성과 달성
유연하고 확장 가능한 솔루션
소프트웨어의 눈으로 본 세상
쉐퍼시스템즈 피스픽킹 애플리케이션의 소프트웨어는 WAMAS 설치에 완전 통합된 구성요소로 작동할 수 있습니다. 그러나 타사 공급업체의 상품 관리 및 자재 흐름 시스템과 함께 자급자족할 수 있는 독립 실행형 시스템으로 원활하게 결합될 수도 있습니다. 피스픽킹 소프트웨어의 핵심 요소는 소프트웨어 모듈인 WAMAS® Vision입니다. 이는 빈(bin)에 들어 있는 품목을 감지하고, 이상적인 그리핑 영역을 파악합니다. 이를 위해 최첨단 이미지 처리 알고리즘과 스마트 AI 기법이 활용됩니다. "실제 세계"를 보는 소프트웨어의 눈은 빈(bin)의 내용물을 묘사하는 3D 카메라 시스템입니다. "실제 세계"와 상호 작용하기 위해 WAMAS Vision은 해당 데이터를 로봇 제어 장치에 전송합니다. 해당 데이터는 로봇 제어장치에서 최적의 픽킹을 위해 그리퍼(gripper)의 물리적 특성과 이동성을 고려하여 처리됩니다. 소프트웨어는 센서와 로봇기술로 구성된 매우 복잡한 시스템에 통합됩니다. 쉐퍼시스템즈는 쉐퍼 케이스 픽킹(Schäfer Case Picking) 덕분에 카메라 및 센서 기술을 다루는 데 필요한 귀중한 경험을 얻었습니다. 쉐퍼시스템즈는 자사 고유 프로세스 역량을 통해 이런 응용분야에 필수적인 자동픽킹에 대한 고유한 기술 노하우, 즉 자동화된 픽킹 셀이 통합될 주변 프로세스에 대한 지식을 견고히 쌓아가고 있습니다.
실제 현장에 적용되는 맞춤형 솔루션
쉐퍼시스템즈의 첫번째 피스픽킹 셀은 2020년부터 북미의 한 제약 도매업체에서 가동되고 있습니다. 셀은 빈(bin) 컨베이어시스템을 통해 공급됩니다. 셀의 설계 방식은 로봇이 2개의 소스 빈(bin)에서 3개의 타겟 빈(bin)으로 동시에 여러 개의 주문 물품을 픽킹하는 다중 주문설계입니다. 이 피스 픽킹셀은 약국 제품 픽킹용으로 최초로 설치되었습니다. 한편, 이 셀을 적용한 약국 제품 픽킹용 사례 7건을 보면 이미 현장에 투입되었음을 알 수 있습니다. 두 프로젝트는 비슷해 보이지만 제품군에 따라 개발의 초점이 달라집니다. 약국 제품의 디자인은 매장에 있는 최종 고객의 기대와 수요를 기반으로 만들어집니다. 소비자의 관심을 끌기 위한 포장 형태는 많은 시스템에서 상당한 문제를 야기합니다. 그러나 쉐퍼시스템즈가 설치한 AI 기반 시스템은 그러한 문제를 완벽하게 해결합니다.
약국 제품에 비해 의약품은 보통 덜 세련된 포장지에 쌓여 판매됩니다. 고객들의 눈을 사로잡지는 못한다는 문제가 생길 수 있지만 의약품의 특성상 완전히 다른 어려움이 존재합니다. 의약품을 픽킹할 때는 오차가 용납되지 않습니다(zero-error tolerance). 그리핑 위치의 선택은 픽킹시 프로세스 안전에 상당한 영향을 미칩니다. 모니터링을 추가적으로 하기위해서는 많은 수의 센서가 사용됩니다. 정교한 통계 및 심층 분석 도구를 사용한다면 로봇 셀의 프로세스를 투명하게 만들 수 있습니다. 시뮬레이션 및 기계학습 절차를 통해 제품군 프로세스를 최적화합니다.
쉐퍼시스템즈의 피스픽킹 로봇 셀은 빈(bin) 컨베이어 시스템의 소형 부품 픽킹과 파우치 로딩 시스템을 위한 표준화된 솔루션을 제공합니다. 매우 유연한 WAMAS Vision 소프트웨어는 다른 물류 환경에도 적용됩니다.
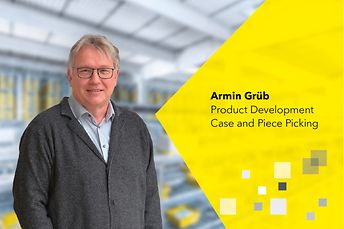
저자 소개:
아민 그룹(Armin Grüb)은 뷔르츠부르크 슈바인푸르트 응용과학대학(University of Applied Sciences Würzburg-Schweinfurt)에서 전기 공학/자동화 기술을 연구했습니다. 그는 크레인 및 인트라로지스틱스 시스템 자동화 분야에서 오랜 기간 경력을 쌓고 독립기업가로서 물류 센터 관리, 이미지 처리 및 시각화를 위한 소프트웨어를 개발했습니다.
아민은 2006년부터 케이스픽킹 및 피스픽킹 시스템 개발을 책임지고 있습니다. 아민과 그의 팀원들은 이미지 처리와 포장 패턴 계산, 로봇 및 복잡한 인트라로지스틱스 시스템 통합 분야에서 실용적 제품 솔루션 개발에 몰두하고 있습니다.
[1] https://ifr.org/ifr-press-releases/news/robot-race-the-worlds-top-10-automated-countries