Rozwiązanie 3 najważniejszych problemów w magazynowaniu w chłodni
Bieżący kryzys zmusił wiele branż do oceny swojej działalności, ponieważ uwypukliły, a nawet pogłębiły znane problemy. Na przykład, brak cyfryzacji lub niedobór wykwalifikowanych pracowników ujawniły nieco kruchy ekosystem. Rozwiązania tych wyzwań są potrzebne szybko, aby pozostać konkurencyjnym i zabezpieczyć przyszłość wielu firm. Magazynowanie w chłodni jest jednym z sektorów, który wymaga nowych rozwiązań.
Z tego powodu operatorzy mroźni zostali zmuszeni do znalezienia nowych rozwiązań. Utrzymywanie status quo nie jest rozwiązaniem. Aby obniżyć koszty energii, przeciwdziałać niedoborowi wykwalifikowanych pracowników i efektywnie zarządzać wymaganiami przestrzennymi dla przyszłego rozwoju, firmy powinny rozważyć częściową lub pełną automatyzację magazynowania lub dystrybucji. Niezależnie od tego, czy chodzi o rozbudowę istniejącego systemu, czy budowę nowego centrum dystrybucyjnego, SSI SCHAEFER oferuje przyszłościowe rozwiązania magazynowe dla logistyki chłodniczej. Ponadto każdy system jest dostosowany do indywidualnych potrzeb klienta.
W naszym Best Practice Guide na temat logistyki chłodni, znajdziesz wszystkie istotne strategie dla przyszłościowych magazynów mrożonek.
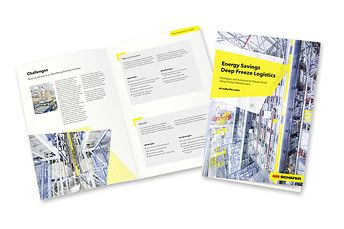
Automatyzacja do rozwiązywania problemów mroźni.
Automatyzacja to sprawdzony i przyszłościowy sposób na rozwiązanie trzech głównych problemów logistyki chłodniczej:
Niedobór wykwalifikowanych pracowników
Brak przestrzeni
Wysokie koszty energii
Minimalizacja czynności wykonywanych ręcznie w chłodni
Brak wykwalifikowanej siły roboczej jest obecnie jednym z najczęstszych problemów. Praca w magazynie często wiąże się z podnoszeniem ciężkich ładunków, powtarzalnymi zadaniami, a także pracą na niebezpiecznych wysokościach. Niedobór wykwalifikowanych pracowników jest szczególnie dotkliwy w magazynach chłodniczych. Warunki pracy w tych obszarach są zazwyczaj mniej atrakcyjne dla pracowników, ponieważ muszą oni spędzać część dnia pracy w bardzo niskich temperaturach.
Staje się to jeszcze bardziej widoczne w przypadku zadań manualnych. Na przykład pracownicy odpowiedzialni za kompletację zamówień i kierowcy wózków widłowych, którzy spędzają znaczną część dnia pracy w pomieszczeniach chłodniach.
Podczas gdy zautomatyzowane systemy pozwolą zaoszczędzić na robociźnie, mają one na celu przyspieszenie przepustowości, zwiększenie gęstości magazynowania i ograniczenie narażenia na trudne warunki.
Innym możliwym rozwiązaniem jest przerobienie procesów obsługi materiałów poprzez dodanie pewnych elementów automatyzacji. Systemy transportowe, magazyny wahadłowe lub maszyny do pobierania z magazynu mogą być wykorzystywane do obsługi, przechowywania i kompletacji pojemników i palet, a także późniejszego transportu nośników ładunku do stanowisk pracy. Dzięki takiemu rozwiązaniu pracownicy są zaangażowani w kompletację zamówień na ergonomicznych stanowiskach pracy, w środowisku o temperaturze powyżej zera. Warunki pracy stają się bardziej atrakcyjne dla potencjalnych pracowników.
Duże zagęszczenie składowania dla mroźni
Ograniczenia przestrzenne to jeden z trzech głównych powodów, dla których firmy rozszerzają istniejące systemy lub zlecają ekspertowi intralogistycznemu sprawdzenie układu obecnych pomieszczeń, integrację nowych rozwiązań z istniejącym systemem lub przejście na pół- lub pełną automatyzację.
wymaga prostej i szybkiej obsługi. Jeśli półautomatyzacja jest obecnie lepszym rozwiązaniem, regały jezdne są opcją. Regały te optymalizują zapotrzebowanie na miejsce i zapewniają dużą pojemność magazynową. Przestrzeń w magazynach głębokiego mrożenia jest droga, więc należy wdrożyć technologię, która tworzy dodatkową powierzchnię magazynową przy minimalnej przestrzeni w korytarzu.
Można również zoptymalizować przestrzeń dzięki w pełni zautomatyzowanemu rozwiązaniu, takiemu jak magazyn wysokiego składowania (HBW). Optymalnie wykorzystuje on całą przestrzeń pionową. HBW to w pełni zautomatyzowany system regałów w połączeniu z maszynami magazynowo-odbiorczymi (SRM), zapewniający wyjątkowo intensywne przechowywanie na najmniejszej powierzchni. Jest to szczególnie ważne w łańcuchu chłodniczym, ponieważ każdy metr sześcienny w magazynie musi być dostosowany do określonych warunków.
Dość często zautomatyzowane rozwiązanie rozwiązuje więcej niż jeden problem. Na przykład, HBW nie tylko wymaga mniej miejsca, ale także zużywa mniej energii dzięki gęstej konstrukcji.
Optymalizacja zużycia energii w logistyce chłodniczego łańcucha dostaw
Koszty energii są jednym z najważniejszych czynników kosztowych dla firm wykorzystujących operacje łańcucha chłodniczego. W przypadku przechowywania ręcznego, regały muszą być dostosowane do szerokości, tak aby produkty mogły być pobierane ręcznie, jak również za pomocą wózków widłowych. Oznacza to, że potrzeba więcej miejsca na chłodzenie i oświetlenie, co zwiększa koszty. Jednak optymalizacja kosztów energii poprzez wdrożenie automatyzacji jest doskonałym narzędziem wspierającym firmy w obniżaniu budżetów operacyjnych i zwiększaniu zysków.
W przypadku pół-automatyzacji dobrym rozwiązaniem są również systemy magazynowania kanałowego. Systemy te oferują kompaktowe rozwiązanie magazynowe na określonym obszarze. Kilka lokalizacji magazynowych jest rozmieszczonych jedna po drugiej w tak zwanych kanałach. Kanałowy system magazynowy jest szczególnie skonsolidowany i wykorzystuje przestrzeń bardziej efektywnie niż zwykłe regały.
W pełni zautomatyzowane systemy wahadłowe i paletowe SRM są budowane z myślą o oszczędności energii. Wiele rozwiązań może nawet pracować w ciemności lub przy mniejszym oświetleniu, co zapewnia bardziej zrównoważone korzyści. Jest to coś, czego nie można osiągnąć w przypadku procesów ręcznych.
Rozwiązania szyte na miarę kluczem do sukcesu dla chłodni
Powyższe rozwiązania są przykładami tego, jak firmy mogą sprostać wyzwaniom związanym z łańcuchem dostaw dla chłodni.
Każde rozwiązanie powinno być dostosowane do istniejącego modelu biznesowego i aktualnych potrzeb klienta.
Idealne wdrożenie dla organizacji będzie oparte na analizie danych. Obejmie ona dostępną przestrzeń, koszty operacyjne i przyszłe cele. Reorganizacja z wykorzystaniem wyłącznie zasobów wewnętrznych może stanowić wyzwanie i właśnie wtedy może pomóc ekspert w dziedzinie intralogistyki. SSI SCHAEFER oferuje każdej firmie, niezależnie od wielkości, niestandardowe rozwiązania, które pozwalają osiągnąć dobrze zdefiniowane cele i kryteria sukcesu.
Zespół ekspertów SSI SCHAEFER może pochwalić się wieloletnim doświadczeniem w zakresie jednych z największych systemów chłodzenia na świecie, ale nasi eksperci wdrożyli również wiele małych i średnich rozwiązań. Każde rozwiązanie jest dostosowane do konkretnych wymagań biznesowych klienta.
Co mówią klienci SSI SCHAEFER
We could have kept the organization as it was 35 years ago – with completely manual operations. We were aware that we were no longer able to compete effectively. The only way to stay in the competition is to use technologies.
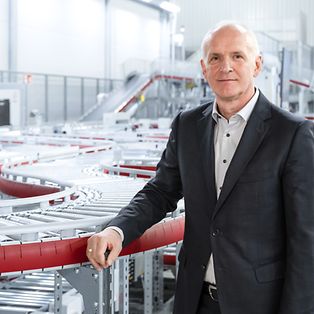
As the first provider of fully automatic deep-freeze solutions in the Philippines, ORCA is the one and only company to invest to that extend in food infrastructure. As a sales head, I saw how customers gravitated to our brand because of the promise of automation. We also experienced first-hand how the market perceives the value that innovation can bring.
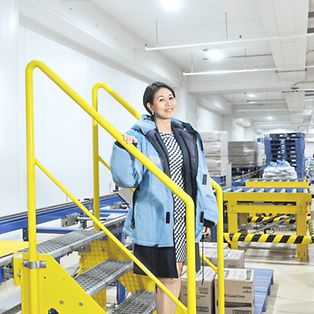

O autorze:
Po wielu latach doświadczenia w firmach logistycznych, w tym na wyższych stanowiskach w zarządzaniu projektami i sprzedaży, Michael Schlacher, dołączył do SSI SCHAEFER w 2021 roku i pracuje jako Senior Sales Manager, Business Development.