Rapid Supply of Spare Parts for SSI SCHAEFER Customers Around the Globe
Neunkirchen/Hranice – SSI SCHAEFER has officially reopened its spare parts warehouse in Hranice, Czech Republic. The new location is located in close proximity to the facility for storage-retrieval machines and boasts significantly expanded production capacity with additional opportunities for growth. In addition to the comprehensive pallet spaces, the spare parts warehouse also has three SSI LOGIMAT lifts with ergonomic workstations for rapid processing of small parts orders.
Since 2014, the previous warehouse on the factory site of SSI SCHAEFER in Hranice has been supplying customers and service technicians with spare parts for automatic warehouses. The trend towards warehouse automation is causing business development to expand. As part of this trend, SSI SCHAEFER planned some adjustments in the storage-retrieval machine production facility. This required changes to the production flow in Hranice and a relocation of the spare parts warehouse. “Thanks to the excellent support from plant manager Robert Selzer and his team, it was possible to find a new location for the spare parts portfolio quickly. The tight time frame made successful implementation of this project a major challenge, but everyone involved helped us meet it successfully,” says Christian Puntigam, Global Head of Service Line Part Services at SSI SCHAEFER.
In an initial step, SSI SCHAEFER prepared half of the available space in an existing building for the new use. The capacity of the pallet rack warehouse was doubled, and SSI LOGIMAT lifts were integrated into the new layout for small parts storage, as well as a crane for handling heavy spare parts packages. The remaining space will be converted to meet the new requirements in the first quarter of 2023. Located a very short distance from the production facility, the new building minimizes the internal transport time for parts and also provides a very efficient goods delivery and collection process for external suppliers.
Rapid Delivery and High Availability Benefit Customer Service
Regional SSI SCHAEFER customers and employees can order all the spare parts conveniently from the SSI Webshop. Incoming orders are automatically forwarded to the warehouse via established IT interfaces, so the picking process can start immediately. In addition to automated order and warehouse processing, the new building also houses the following activities: incoming goods receipt and quality inspection, picking, pre-assembly, organizing transport and issuing customs documents. In the future, it will also be possible to carry out minor repair work at.
The spare parts warehouse portfolio will follow a so-called “highly dynamic warehouse management process,” with the clear objective of integrating highly critical, high-priority parts with dedicated flexible stock. The significant reduction in delivery times and high availability of the required spare parts will also increase customer satisfaction.
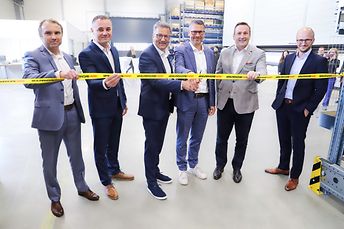
From left to right: Jan Skypala, Spare Parts Team Leader, Hranice; Radek Nemec, Spare Parts Department Head, Hranice; Elie Zita, SVP of the Customer Services Business Unit; Christian Puntigam, Global Head of Part Services; Robert Selzer, Head of the Hranice plant; and Gerald Insupp, Global Head of Spare Parts Management, at the official reopening of the spare parts warehouse in Hranice, Czech Republic.
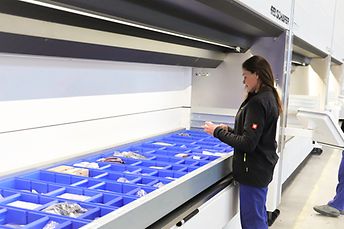
SSI LOGIMAT lifts store all the small parts for rapid ergonomic picking.