As powerful as their warehousing software:
The advisory expertise of SSI SCHAEFER
The initial situation for Robert and "Freizeit Handels GmbH" was extremely tricky, when they reached the joint decision to make changes to stock handling and therefore also to warehouse management: Due to the rising demands and constantly increasing throughput, the same work required comparatively greater effort than before. The increasing costs of storage began to eat into additional profits. However, this is now water under the bridge and the customer – with Robert at the helm – appears thoroughly delighted with the results of this decision.
As the warehouse manager and authorized signatory, Robert is responsible for both the international e-commerce of "Freizeit Handels GmbH" and the outbound delivery of all products – in the many new and existing stores domestically and in neighboring countries. Recently, he has been preparing for the changeover to a new warehouse management system. The new system had become an urgent requirement because the interaction between the stock lists and the extremely straightforward, self-programmed warehouse software was resulting in an increasing number of duplications with the growth of the business. The weekend before last, Robert and his employees, together with the project team of the software supplier SSI SCHAEFER, performed the commissioning from Friday to Saturday. All those involved had prepared themselves meticulously and the process ran like clockwork.
Afterwards, Robert had to admit that he experienced occasional concerns about how everything would work out during commissioning of the new warehouse management system. Whether unforeseen challenges might perhaps arise that had not previously occurred to him, or indeed the software consultants from SSI SCHAEFER, who supported him with immense commitment. When choosing the system, Robert deliberately opted in favor of this software supplier. During the preliminary discussions, he and his colleagues had gained a convincing impression that many of the new demands had already been implemented in the WAMAS® software, and that the software consultants possessed an impressive level of expertise and the experience required to successfully realize the additional requirements.
During the course of the project, it became apparent that Pauline – the lead software consultant from SSI SCHAEFER – not only brought extensive experience with her to the process, but also that she was highly receptive to the warehouse requirements and the warehousing operations at "Freizeit Handels GmbH". The changeover to the new system realized by Pauline and her team was repeatedly scrutinized within the framework of common tests performed on the test bench. The diligent tests showed where the odd ambiguity had crept in during discussions, and it was therefore possible to quickly eliminate any potential hurdle in advance. Pauline made a highly competent and extremely friendly impression throughout the course of the project. And if the situation ever demanded it, she resolutely and consistently pointed out the way forward – specifically and always with the intention of attaining the best possible result from this project. With her impressive feel for the day-to-day activity in the warehouse, Pauline played a major role in ensuring that the introduction of the new system ran smoothly and successfully.
How exactly did the "warehouse management" project take shape?
It became increasingly apparent over time that the old software was no longer able to satisfy the increased demands of customers, shipping services, and the newly opened stores. At the same time, a number of suppliers were offering services that would have brought a great deal of simplification. However, they were unfortunately unable to tap into the potential of these with the old software. Finally, Robert and the management of "Freizeit Handels GmbH" decided to initiate a project to introduce new warehouse management software.
During the preliminary phase it was primarily necessary to gather all the requirements and invite various providers to present their software and the project process. SSI SCHAEFER succeeded in impressing on all levels with its WAMAS® warehouse management system, and therefore secured the order. Before signing the order contract, Robert got to know the SSI SCHAEFER project team, which consisted of project managers, software consultants, and software developers – with Pauline heading up the team as lead software consultant.
As the primary point of contact, Pauline always listened to all of the concerns expressed by Robert and his warehouse team. Regardless of whether these were legitimate worries or unplanned stumbling blocks, Pauline always paid close attention and listened carefully, and made extremely productive suggestions on how to successfully realize specific requirements. Through her outstanding commitment, she impressively demonstrated that dedicated software consultants are much more than dutiful translators between warehouse operations and programming. By applying their experience and judgment, understanding and foresight, and in particular their expertise, they are able to make the difference in any project – and ensure the outstanding implementation of new warehouse processes.
At the start of the project, the functional specification was drawn up in close cooperation with Pauline. This contained a highly detailed definition of how the future warehouse processes would look. If Robert or one of his team members wanted to deal with a topic rather too hastily, Pauline demonstrated great patience and persistence – as and when the situation demanded. It frequently transpired that the warehouse processes, previously described only briefly, were somewhat rough around the edges and were not entirely clear to individual employees even before this project began. Up to this point, they had been able to dodge their way out of the situation, for example by manually correcting incomplete data retrospectively.
The new system now controls all of the warehouse processes. Its precise process control not only avoids errors, but also makes processes more reliable. This requires a precise specification of the processes beforehand, which must then be equally carefully observed during the stages that follow. Goods-in, picking, packing, and transfer for outbound delivery were dealt with in detail within the project framework. Many different efficiency potentials were identified during intensive discussions, which led to additional optimization of the warehouse processes.
Pauline paid particularly close attention to the storage and replenishment processes. The so-called flow of goods forms the backbone of all processes in the warehouse. The effectiveness of a warehouse is largely dependent on its flows of goods. Several intersecting flows of goods can be defined within the WAMAS® warehouse management system, and assigned to individual or several selected products. Pauline and her project team succeeded in keeping the flows of goods simple and coherent, although it was also necessary to take a number of special functions into account. Experience has shown that such added requirements are always of crucial importance, because the warehouse staff are ultimately required to work with these flows of goods on a daily basis. Depending on requirements, flows of goods can be adjusted and new products that have been added to the warehouse can be additionally assigned to these. The same applies, for example, if there is a change in the terms of delivery applicable to products.
Pauline modeled and parameterized the warehouse within the software to reflect the required processes. Once the necessary add-ons had been programmed in the software, the first step was to test these internally with her team. And after the warehouse had been mapped in the software, joint testing commenced together with Robert and his co-workers. At the start of the test phase, Robert and his colleagues received comprehensive training on the new system. Afterwards, they went through all the functionalities and the user guidance in detail with Pauline and her team. At the same time, minor software adjustments were implemented to further enhance user-friendliness, and these were mapped in the software within a very short time. During testing, it transpired that one of the many processes was not yet fully on point. However, this was also swiftly optimized with Pauline's help. Robert was visibly impressed with the meticulous way in which Pauline conducted the tests, and was also extremely happy with them. After all, informative tests keep the risks of possible complications in the warehouse to an absolute minimum.
All tests were concluded two weeks prior to commissioning the new system. And the script containing all of the information for the go-live procedure was also complete. All details were checked and run through several times on the test system. System introduction was optimally prepared, and took place under careful observation with the utmost calm professionalism. Three weeks later, Robert's signature confirmed acceptance and therefore also successful completion of the project. As there is inevitably always something in a warehouse that requires optimization, Robert introduced a continuous improvement process in which all warehouse employees participate.
About the author
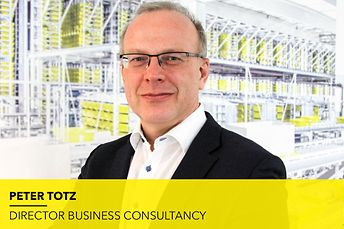
Peter Totz works as Director Business Consultancy at SSI SCHAEFER.
His career began as a project engineer, data analyst and simulation specialist in Graz. With intermediate steps in production planning and as a logistics consultant, he worked as a senior consultant and project manager for many years. Later, he was responsible for business development in Latin America before taking over the lead of the globally active Business Consultancy Group.