From a Temporary Storage Facility to a Global Logistics Center
SSI SCHAEFER now supplies spare parts even faster – all from a single source
With a state-of-the-art warehouse in Hranice, Czech Republic, SSI SCHAEFER has reached a major milestone in its spare parts service. Christian Puntigam, Head of Parts Service Line, and Radek Němec, Team Leader for Spare Part Management, Hranice, followed the project from the initial idea all the way to implementation. In this interview, they describe how they achieved a whole new level of efficiency by optimizing the existing warehouse – and why, despite great success, their work is still far from done.
What’s the purpose of the new warehouse in Hranice?
Christian Puntigam: The warehouse in Hranice stocks spare parts for the entire SSI SCHAEFER product portfolio; from there, they ship to customers all over the world. At present, it handles just under 7,000 different items, from the smallest gaskets to entire assembly groups, with an inventory valued at several million euros.
Radek Němec: This warehouse not only stores spare parts for products from the factory in Hranice but also from other SSI SCHAEFER production sites. That means a very large percentage of our spare parts portfolio is now available in one central location.
Why did you opt for a central warehouse?
Christian Puntigam: So we can offer our customers even better delivery performance and make our internal processes even more efficient. By bundling inventory, we can significantly reduce the amount of time between receipt of an order and delivery to our customers. With its proximity to the factory, established processes, and good strategic location, the Hranice site was the best choice for our competence center.
How did you update the existing warehouse in Hranice for its new use?
Radek Němec: The first step was converting hall 12, which had been used for temporary storage up till that point. We doubled the capacity of the pallet rack warehouse and integrated three SSI LOGIMAT® vertical lift modules into the new layout, along with a crane for handling heavy packages. In the second step, we then relocated all the products from the warehouse in Giebelstadt, Germany, to Hranice.
Christian Puntigam: We completed the entire conversion project in just a few months without interrupting operations. That would never have been possible without the amazing support of our service and factory teams – everyone gave it their all.
What’s the procedure for ordering spare parts from the new warehouse?
Radek Němec: Our customers can select the spare parts they need easily in the SSI SCHAEFER Web Shop. The order is processed in Hranice and ships either right from the warehouse or, for items that are rarely ordered, through external partners.
Christian Puntigam: That way, customers get spare parts service all from a single source. We also handle customs, transport, shipping, etc.
The warehouse has been in operation since the end of 2022 – are you already seeing the early signs of success?
Radek Němec: Absolutely! We used to be able to process about 2,800 orders a year, but this year, we’re expecting up to 5,500 orders and around 5,000 items a month. So we’ve basically doubled our output, increasing the value of the Hranice site enormously.
Christian Puntigam: Of course, the biggest benefit is to our customers. Revamping the processes has made ordering spare parts even faster and easier.
Is the project now complete? Or do you have more plans for the future?
Christian Puntigam: We’re very satisfied with the performance of the warehouse in Hranice, but we want to keep improving nonetheless. Besides transferring a relevant portfolio of spare parts from Graz in Austria, which is scheduled for 2024, we’re already working on optimizing the material flow even further. We’re performing a detailed analysis to identify what paths we can shorten within order picking and what processes we need to speed up in order to make our operations sustainable, customer-oriented, and more efficient. That’s our goal.
SSI LOGIMAT – Store Small Parts, Keep Track of Everything, and Save Space
SSI SCHAEFER’s SSI LOGIMAT vertical lift module can be likened to an oversized drawer cabinet with two rows of trays. Between the two rows, a lift system pulls the individual trays out and moves them to the operator opening, where operators can safely pick goods.
Thanks to an intelligent user interface, controlling the lift rack is simple and intuitive. The SSI LOGIMAT vertical lift module offers some helpful enhancements that make picking significantly easier. For example, LOGIPOINTER can indicate the correct position with a laser pointer. By the way: Each tray can be individually loaded with bins or cartons–or used without any kind of partitioning.
SSI LOGIMAT vertical lift modules are used in many industries for storage and retrieval of various kinds of goods:
eCommerce
Healthcare & cosmetics
Retail & wholesale
Industry
Automotive
Modular vertical lift systems have many different applications:
Small parts storage
Item management
Buffer storage for production
Order preparation
Storage and picking of service parts and spare parts
Storage of unfinished/semi-finished products
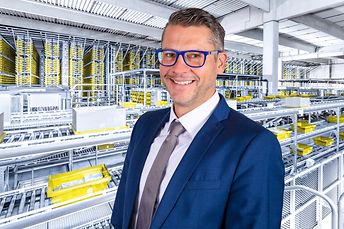
Christian Puntigam, Head of Parts Service Line at SSI SCHAEFER: “We’re performing a detailed analysis to identify what paths we can shorten, what processes we can speed up, and how we can increase overall efficiency even further.”
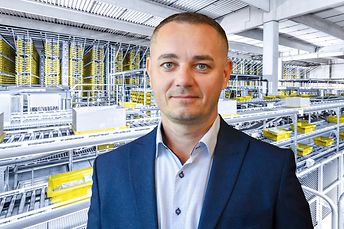
Radek Němec, Team Leader for Spare Part Management, Hranice, at SSI SCHAEFER: “We used to be able to process about 2,800 orders a year, but this year, we’re expecting up to 5,500 orders and around 5,000 items a month. So we’ve basically doubled our output, increasing the value of the Hranice site enormously.”