Mobile Racking for Maximum Storage Density
Freely scalable mobile racking systems are the perfect solution for maximising warehouse capacity and providing full flexibility in handling operations. Thanks to his many years of market experience, David Eisenhut from SSI SCHAEFER understands how much deep-freeze logistics companies, for example, benefit from this. In this interview, the expert for dynamic intralogistics solutions provides insights into how mobile racking can be integrated into warehouse processes, when automation is worthwhile and how the systems help to save energy costs.
David Eisenhut, we are standing here in front of an ESX mobile racking. Please explain it briefly.
With pleasure. With a bay load of up to 32 metric tons, the ESX belongs to the group of heavy-duty mobile racking systems. The carriages are designed for loads of up to 600 metric tons. This makes them equally suitable for storing pallets [ESX] and heavy long goods [ESZ]. The rack heights can be designed to match the lifting height of the forklift systems used. With this design, systems of up to 16.5 meters in height can be constructed; always provided that the operation is not exposed to any earthquake risk.
What are the advantages of such a mobile racking in the real world?
Since only one working aisle is needed, we can make a 45 per cent space saving. Compared to static rack systems, the capacity of the hall can be increased by over 90 percent, achieving maximum storage density. Additional benefits are also gained in the efficiency of warehouse processes. For instance, the mobile racking control system can be programmed to optimise picking processes, thus minimising travel times. The advantage here is that the aisles between the carriages can be opened flexibly. This ensures that the warehouse transport systems always have direct access to all storage locations, effectively avoiding the relocations often required in other compact storage systems.
In essence, the aim is to minimise the space requirements of the system and to achieve sufficient degrees of freedom for picking. Which companies place particular emphasis on these advantages?
Our customer projects show that there are four main areas of application in which the benefits of a mobile racking system are particularly high. Top of the list is certainly temperature-controlled logistics. If you operate a deep-freeze warehouse, you are managing operating costs that necessitate optimum use of your storage space. Increasing the amount of goods stored in the warehouse reduces the energy required to regulate the temperature-controlling volume. The resulting energy savings shorten the ROI of both the rack system and the refrigeration technology. On top of all that, expanding capacity can also significantly benefit your core business. After all, it allows you to take on more orders and increase the added value of your warehouse.
Logistics service providers should also be interested in this, right?
Definitely. This is also evident from our practical experience with customers. Incidentally, third-party logistics providers (3PL’s) are particularly excited in this. This is because, in addition to maximising capacity, these providers are also interested in the greatest possible flexibility when it comes to handling. After all, the core competence of 3PL lies in being able to serve various customers precisely. The mobile racking system used must offer sufficient options to accommodate the load carriers required by the end customers. It is also important to keep an eye on picking times in order to meet the agreed service levels. The interplay between capacity maximization and flexibility in handling also becomes particularly exciting when talking about 3PL deep-freeze logistics companies, such as our Dutch customer Grolleman. In warehouse environments such as these, mobile racking technology makes the most of its potential benefits.
With temperature-controlled logistics and the 3PL sector, you have already addressed two key fields of application. Where are the other two?
On one hand, there are warehouse locations where expansion is no longer feasible, necessitating a focus on optimizing the use of available space. This issue is particularly relevant for customers in built-up areas. And on the other hand, mobile racking technology is also ideal for companies in the manufacturing industry, where space-saving storage is often more important than the rapid turnover of goods. Incidentally, this is definitely something that no one should ignore when considering the use of mobile racking technology. This type of system is primarily designed to optimize storage. As already shown, requirements from the picking section are also taken into account. However, this only ever happens to a certain extent. The optimization efforts focus on the storage capacity rather than the handling volume.
When does the investment start to pay off?
That is very customer specific. Generally speaking: the greater the location costs, such as real estate prices and trade taxes, the faster a mobile racking system proves to be cost-effective. The same applies to the infrastructure and energy costs. The greater they are, the more advantageous it becomes to maximize the storage density of the warehouse. As a rule of thumb: mobile racking systems are roughly twice as expensive as alternative static systems. Regardless of this fact, the use of mobile racking can pay for itself very quickly, depending on the specific warehouse environment.
Let us now take a closer look at the practicalities. Starting with the topic of safety. What does SSI SCHAEFER offer in this field?
First and foremost, it is about immediately recognizing any obstacles in the working aisles and acting accordingly without delay. Our systems have a multi-level warning system for this specific purpose: Access to the currently open aisle is prevented by light barriers that are installed on the floor in front of and behind the mobile racking blocks. If a light beam is interrupted, the entire system stops. Further light barriers are fitted on the longitudinal sides of the carriages at foot height. This additional protection system instantly detects if goods fall into the working aisle while a carriage is in motion, thereby ensuring a rapid response. In this case, too, the system stops immediately. Needless to say, we also comply with all regulatory requirements. This also applies to the fire protection section. Moreover, we also guarantee safe system operation in earthquake-prone regions. To this end, we supply our products in an earthquake-proof design.
In seismically active areas, preventive maintenance is certainly a very special topic. But, that aside, this type of system is already exposed to great risks of wear. How does SSI SCHAEFER deal with this?
That is definitely a justified question. We have taken a whole range of factors into account to protect the mobile racking, which weighs several metric tons, the supporting rail system and the warehouse floor against wear. To list all of these technical precautions would certainly exceed the scope of our discussion. Nevertheless, I would like to highlight five key aspects. Let us start with load distribution. With a four-wheel traveling unit, we achieve the best possible distribution of the load on the floor. At the same time, we optimize the load on the wheels. Each wheel is fitted with four raceways with deep groove ball bearings, which help to prevent unilateral bearing loads. We also use distance sensors to ensure that the carriages are always positioned parallel to each other along their entire width – regardless of whether they are parked or moving. The electric motors of the rack carriages, featuring two gear stages with direct gear, also ensure smooth and consistent movement. The rail profiles on which they run are made of high-strength steel with a specific profile that can be firmly embedded in the floor slab of the warehouse. All of this helps to minimize the maintenance costs and downtimes of the rack systems.
To what extent can the system be automated?
If requested, fully automated operation is possible, in which the system is synchronized with automated guided vehicles (AGVs) and all processes are controlled digitally by fully integrated warehouse management software. Since the software maintains an accurate map of the current goods locations at all times, it can open the mobile racking as needed by the order and direct the best available AGV for loading and unloading. Alternatively, semi-automatic and, of course, fully manual operation of the system is also possible.
What are the software requirements for this?
None from the customer's perspective to start with. Thanks to their programmable logic controller (PLC), our mobile racking systems can always be used as a standalone solution, after all, each position on the rack crossbeams is provided with a barcode. Employees use handheld scanners to read this barcode and accordingly report the storage or picking of the loading goods to the warehouse management system.
How widespread is this type of system integration?
At present, it is still the norm. That said, the number of users who want deeper integration is growing all the time. The aim is to increase the level of automation in warehouses. To this end, we offer a transport control center that synchronizes with the order control system, regardless of whether this is an ERP, MFS or MRP solution, for example. The control center informs the warehouse transport systems about which specific loads to handle, where and how. The labor performed is also acknowledged by the control center. Yet another automation step can be to give the commands to open and close the aisles directly from the control center.
An important prerequisite for the use of automated guided vehicles.
Absolutely. Which of course brings us very close to fully automated operation of the warehouse systems. But regardless of how extensive the roadmaps of our customers are for a specific use case, the actual automation is always built on the standard interfaces provided by our solutions This allows our customers to focus on designing the warehouse processes without having to also adapt the supporting IT systems.
Mobile racking can be combined with other solutions from the SSI SCHAEFER portfolio to achieve additional increases in efficiency. In which section is demand currently particularly high and why?
We are certainly seeing a particularly high level of dynamism in IT integration, for which we offer a broad portfolio of software solutions that can be used to plan, control and optimize the entirety of warehouse processes and functions. The aim is to achieve a 360-degree view of all internal goods and material flows. This level of transparency allows users to manage ongoing orders in line with processes and to completely utilize warehouse facilities. This enables you to fully exploit the automation potential of mobile racking. Especially as we are able to also supply the most suitable automated guided vehicles and the appropriate load carriers. Added to this is our wide range of pallet, cantilever and long-span racking, which enable the modular design of carriages to create customized solutions.
Finally, let us draw a conclusion. At its core, what makes mobile racking an attractive choice for customers?
The space-saving nature of the technology leads to the highest possible storage density. If you want to utilize the capacity of your warehouse to the maximum and need as much flexibility as possible when it comes to handling goods, a mobile racking system is simply the best choice. Especially as there are a variety of automation options that can be used to improve the efficiency of the warehouse processes step by step. The potential savings in energy costs should not be overlooked either. Deep-freeze logistics companies gain the most from this by minimizing the temperature-controlling volume of their warehouse. However, the low lighting requirements of the systems and the high efficiency of the electric motors installed in them are also relevant. All of these factors help companies to reduce the warehouse operating costs and noticeably shorten the payback period of the mobile racking.
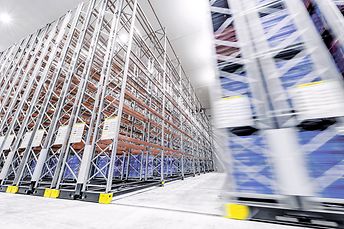
Mobile racking from SSI SCHAEFER enables a bay load of up to 32 tons.
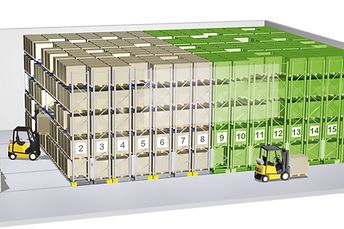
Storage capacity can be significantly increased by using mobile racking.
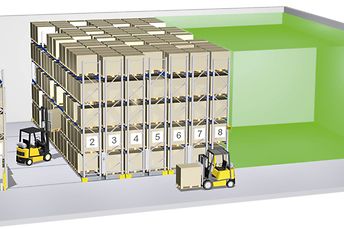
Mobile racking requires only a fraction of the storage space needed by conventional racking.