Future-proof solution for flexible small parts storage
No matter whether it is due to rapid growth, supply bottlenecks or absence of employees – the importance of flexibility in small parts storage becomes apparent in cases of unforeseen events. How do you ensure delivery capacity, even in dynamic times? If automation is the solution, what measures can be implemented in a small parts warehouse with only minor investment? How flexible and scalable are these systems?
Many companies only recognized the importance of transparency and flexibility in intralogistics during the corona pandemic: Problems in global supply chains led to limited availability of products. Volatile business developments and shifts of sales channels caused further delivery difficulties. Lack of staff or changing business models caused further problems.
In retrospect, key drivers affecting intralogistics can be categorized into four groups:
1. Material availability
2. Sales fluctuations
3. Staff availability
4. Business logistics adaptations
1. Ensuring material availability
To ensure material availability in the warehouse, the following principles must be observed and applied:
Having a clear warehouse structure and transparency of stock
Avoiding shortages and inventory differences
Ensuring safe storage and error-free picking
Transparency and having an accurate inventory of all stored items are the most important prerequisites for ensuring material availability. The “no picking without booking” principle applies; only consistent and timely booking processes can avoid shortages. This requires a clear warehouse design and a fixed storage location for each item, which is only possible in an efficient and secure way with IT support. The availability of an item should also be visible to other business areas or the online shop using an interface to the ERP system.
The vertical lift SSI LOGIMAT® fulfills the requirements of a transparent small parts warehouse and delivers efficient, error-free picking. It provides space-saving storage of small parts in bins or cartons on trays. A lift in the center of the system transports the desired tray to the access opening. The storage lift ensures complete transparency of all stored items and can be connected to the ERP system via an interface.
Compared to a static rack warehouse, the advantages of compact warehousing add up: Thanks to the dense storage of the trays, storage capacity can be increased by up to 90% compared to a static rack warehouse. In exact figures, on a 10 m² footprint, a 7.5 m high SSI LOGIMAT® provides 150 m² storage surface. A bin concept, especially developed for SSI LOGIMAT® ensures transparent, safe and clean storage of items on each tray. The user interface, with touch screen facilitates, provides a clear and ergonomic operation. The individual compartments for storage or retrieval are indicated to the operator by a laser pointer. Picking errors can be reduced by 50%, while searching times in the warehouse can decrease by up to 90%. SSI LOGIMAT® ensures accurate booking processes, high transparency and safe storage as well as increased storage capacity.
2. Being prepared for sales fluctuations
Volatile order situations are characterized by short-term order peaks alternated by low demand or even downtimes. Many companies still have an unconventional way of organizing their intralogistics which makes managing these fluctuations difficult.
Advantages and disadvantages of manual warehouses at a glance:
Advantages of manual warehouses:
Low investment costs
Easily extendible, possibly by platforms onto a second or a further level
Technical performance is scalable by staff deployment, if necessary
Wide range of items can be stored
However, there are also disadvantages:
High space requirements for racks and aisles
Non-optimal usage of space
Inefficient time usage due to required walking distances
Performance/productivity is dependent on staff availability
Greater personnel costs
This is coupled with the disadvantage of manual warehouses having primarily non-ergonomic activities, such as picking items from lower shelves or shelves that can only be reached with climbing aids, and the higher error rate compared to semi-automatic and automatic systems.
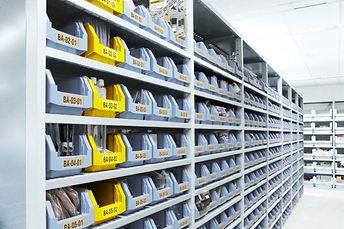
Even well-organized static rack systems do not make optimum use of the available storage space – particularly of the height or with wide aisles between the racks.
With a growing number and variety of items, manual warehouses can only accommodate the changes caused by sales fluctuations to a certain extent. Particularly in e-commerce, with fast deliveries and numerous orders, with only a few positions that must be picked in next to no time, manual warehouses have limitations.
When searching for the most suitable automation solution, it is all about finding the perfect combination of flexibility, scalability, the degree of automation and cost. The variety of automated miniload systems on the market ranges from carousel or robotics systems to high bay warehouses with storage-retrieval machines or shuttle systems. Automatic conveyor systems and goods-to-person work stations must be planned and integrated. Alongside the introduction of automation there will be corresponding business operations and maintenance efforts which will either be the responsibility of system suppliers or in-house technicians. These complex systems are suitable for business models with a wide variety of items and high turnover. However, for a number of applications and companies, the complexity and investment costs of these automated miniload systems are not an economic solution.
In order to prepare warehouses for sales fluctuations, companies should consider the following aspects:
flexible storage technology,
scalable storage technology and
short Return on Investment (ROI) periods.
With these considerations companies can flexibly adapt their processes and technical performance to ensure economic success. For short-term increases in storage capacity, the selected technology should also be easy and quick to install, have future viability and be able to be integrated with other, existing technologies, for example for transport orders.
The storage and picking system SSI LOGIMAT® fulfill the above mentioned requirements and combines the benefits of manual and automated systems.
It is a flexible system that is scalable in performance, height and capacity. In time of low workload, one operator can work on several SSI LOGIMAT® lift modules simultaneously, while several operators can pick during peak times. Thus, picking performance is flexible and can deliver to up to 450 picks per hour and user. Different picking strategies can be applied from Single Order Pick to several pickers to Multi Order Picking. Several vertical lift modules can be integrated in no time with the plug&play principle; including delivery time and IT integration, this can be as quick as 3 months. Picking strategies and services at a glance:
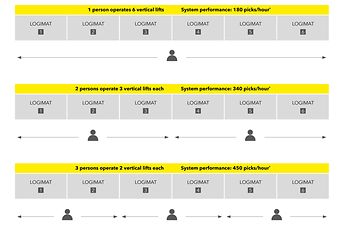
Applying the SSI LOGIMAT® for automation, the system performance can be flexibly adapted to the order profile at any time through the number of devices and operators.
The ability to plan investments in intralogistics is of utmost importance. In addition to the investment cost, short planning and ROI periods are also crucial.
A fast ROI can be achieved by savings in:
Personnel costs
Occupancy and energy costs
Picking error costs
Inventory and stock errors
3. Managing staff availability
Lack of qualified staff has been one of the main challenges in intralogistics for many years. Finding new staff for work stations or additional workforce members has been and continues to be difficult. The corona pandemic has increased the risk of having to accommodate staff shortages due to illness or quarantine regulations including current hygiene guidelines and distance regulations.
Companies have to deal with the following problems in personnel availability:
Shortage of skilled workforce
Fluctuation of employees
Demographic changes
Illness and staff shortages
Staffing limitations are further affected by changing living and work environments. For this reason, companies should consider adapting their intralogistics and, if necessary, investing in automation technologies in order to maintain their ability to meet customer delivery expectations. A higher degree of automation in the warehouse streamlines the processes and makes companies more independent of staff and operational issues. In return, the need for a highly skilled workforce for the operation and maintenance of the systems as well as for software specialists is increasing.
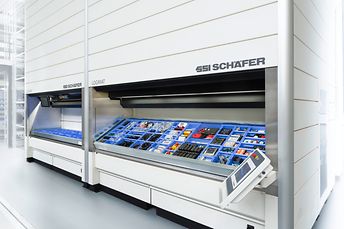
The SSI LOGIMAT® offers intuitive usability for accessing automation.
The ease of use of the SSI LOGIMAT® means companies can flexibly deploy their staff. Operators can be trained on SSI LOGIMAT® in about 10 minutes. Additionally, the SSI LOGIMAT® is ergonomically designed to tilt product storage trays for comfortable picking of items. This facilitates easy item or order handling and reduces back pain.
4. Handling business logistics adaptations
The increasing dynamics of the markets require companies to be adaptable. During the global pandemic, at times companies quickly changed their production, for example, and manufactured ventilators and air purification systems, due to the high demand. In addition, e-commerce experienced strong growth, while bricks-and-mortar sales declined. Additionally, individual everyday products in food retail were in high demand.
All these developments and swift changes have had a massive impact on logistics – whether through additional products, storing spare parts for old products, changing the product portfolio or changing the distribution channels. Therefore, modern warehouses have to be flexibly scalable and adaptable to stored goods, services and processes. This means they must:
be independent of product geometry and load carriers,
have scalable performance – upwards as well as downwards
and have scalable processes through modular technologies.
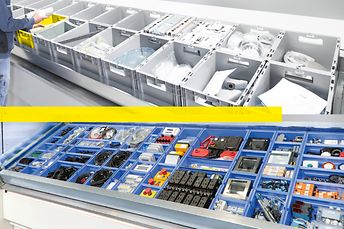
Vertical storage technology adapts to a variety of items using specifically developed bins.
Conclusion
The use of vertical lift modules in small parts storage and picking, helps companies to act both flexibly and efficiently at the same time. Automation options prepare companies for unexpected events so that they can continue to deliver with comparatively low investment costs and prompt ROI. In addition, it is easier for companies to maintain their efficiency and outputs regardless of unexpected staffing limitations. An effective intralogistics system contributes significantly towards business success.