How to Manage Cold Storage Warehouse More Efficiently
Cold chain solutions are required at every stage of the supply chain, from the point of production, through manufacturing and storage to wholesale and ultimately to retail or catering establishments and to people’s homes. In this climatic world that we live in today, higher temperatures and more extreme events are affecting the cost and the demand for cooling across the world. Globally, the growing requirements for cooling solutions while simultaneously reducing the energy and carbon emissions associated with storage and distribution are at an all-time high. Over the last three years of the pandemic crisis, it has further accelerated the demands for storage and the requirements for B2B and even more B2C performance and highlighted the importance of cold chain in many business sectors worldwide – notably, the Pharmaceutical and the Food & Beverage verticals.
Even before the crisis, changes in eating habits, all year-round availability of food, the rise in single households and the growing demand for convenience products have led to a significant growth in the deep-freeze and temperature-controlled food segments. Companies that have demonstrated the resilience of their business and toward managing the health and safety of the employees (regulated working hours in cold temperature zones) have adapted fast in the adoption of warehouse automation and toward the shift in consumer buying behavior.
Managing a cold storage warehouse efficiently poses serious hurdles because the storage of perishable and sensitive goods requires special handling and monitoring. Most logistics and operation managers seem to face an awkward situation in developing an efficient and cost-effective material flow infrastructure, mainly because the planning process must occur before the construction of a warehouse – whether a temperature-controlled or an ambient warehouse.
To better manage a cold storage warehouse efficiently, we need to understand the factors that should be considered before planning a cold store operation.
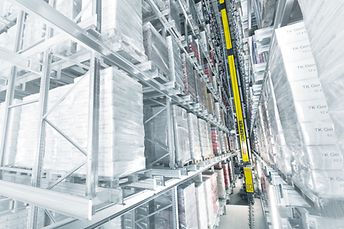
Retrofitting or Designing a Green Field Facility
A greenfield project may make the most sense when starting from nothing or expanding rapidly since future-proofing the facility improves the ability to respond to current and future business requirements. While such facilities may be further away from urban areas and it might be harder to hire skilled labor, it is an opportunity to integrate automation equipment. It not only transforms the workplace and increases productivity, but it also better manages the energy usage within the facility.
Akin to greenfield, retrofitting can help to revitalize urban areas. Through grants that are sometimes available, this option can be a cost-effective way to improve the current operation. However, to upfit for meeting building codes, longer construction and installation times are expected, especially if slab usability is an issue. These consequences may, amongst others, limit throughput or result in higher energy consumption.
Proper Planning - Doing More in Smaller Spaces
Cold storage warehouse temperatures are broad, typically ranging from -34°C to 0°C but also consider chilled environment of up to 21°C. At the preliminary phase of planning the warehouse layout, selecting the right storage system that enhances the cooled air circulation while increasing the storage density in the given footprint of the cold storage should be considered.
Semi-Automated Solutions – Channel Storage System VS Mobile Pallet Racking System
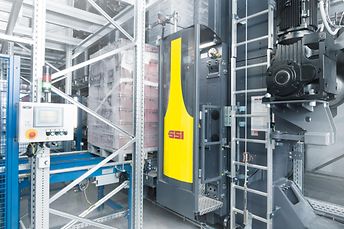
Semi-automated drive-in racking systems are typically deemed as an easy step towards ‘Automation’. The highly compressed channel storage method uses channel vehicles such as the SSI Orbiter® and a corresponding docking station to put goods into, and remove them from storage, and guarantee higher space utilization and throughput. In line with either the Last in-First Out (LIFO) or the First in-Last Out (FIFO) principles, the automatic reorganization of the channel complies with the logic of whether the storage and retrieval of the pallets is from one side of the rack, or two sides of the rack. Since the different storage levels can be accessed individually the filling ratio is higher than a conventional drive-in racking system, and it is more efficient and ‘safer’ as it eliminates the need for forklift operators to access the pallets directly.
The Mobile Racking Storage Systems are racks built on a mobile base-plinth and guided by rails on the floor. Driven by electric motors, the mobile base moves along the rails to open one or more aisles to access the racks. This creates new storage capacity in the spaces otherwise used for permanent aisles (increasing storage capacity by up to 85%) yet allows 100% access to goods easily. Integrated with smart lighting control options, the connected lighting system only illuminates when people are present and within the open aisle, providing a new degree of control over electricity use. With the night parking options, the system separates all bases during the non-working period to enable excellent cold air flow circulation. To promote a safer warehouse working environment, all the systems are supplied with emergency-stop buttons, photoelectric access barriers, manual release systems, proximity sensors and safety light barriers. All these features ensure that the operation remains smooth, and the employees work safely inside the warehouse.
Implementing Automated Systems From a Single Source
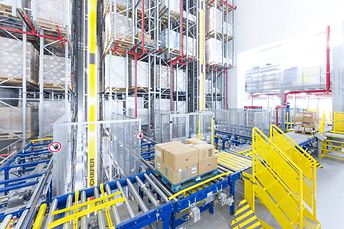
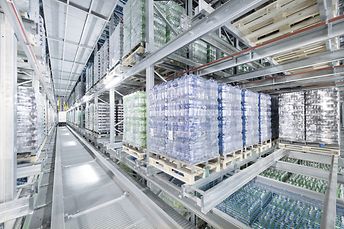
Most frozen goods have strict schedules and cannot sustain any form of delay in storage or transportation. It is important to ensure the storage system can handle incoming goods and can cope with the upticks in consumer demand, seasonal production, and holiday crunches. Storage & retrieval machines (SRM) and shuttle systems meant for pallets, trays, or bins and cartons, but also autonomous AGV/AMR machines are key elements. A fully automated storage system installed within a high-bay warehouse, connected with conveying systems and intelligent software provides seamless integration into a cost-optimized logistics chain. Here is a quick breakdown of some of the basic storage concepts:
Storage & Retrieval Machines for Pallet Loads – The Green Crane Technology makes SSI SCHAEFER’s Exyz storage and retrieval machine (SRM) for pallets impressively energy-efficient. Conducive for various climates use, the SSI Exyz is compact, not only fulfilling the goals of maximizing available space (use of vertical space up to 45 m high), but it is also an effective warehousing solution for large portion of stored goods with easy accessibility (single-deep, double-deep, and multiple-deep channel storage). In combination with the SSI SCHAEFER ORBITER satellite, this is a kind of a ‘step-up’ for semi-automated channel storage solution and can achieve extremely high storage density.
Shuttle Solutions for Pallets – Highly dynamic and future-proof, these are the next step of an SRM working with a satellite unit for automated channel storage. With a separate lifting device and multiple single- or multi-level shuttles like the SCHAEFER Lift & Run Shuttle System (SLR), these multiply the performance of an otherwise single SRM, whilst providing the same high storage density in satellite operated channel storage. The high throughput ability supports high performance environment, and most of all semi-automatic Goods-to-Person case picking.
Shuttle Solutions for Layer Trays: Pallets broken down into layers and stored on trays, allow extreme performance in storage and retrieval process, particularly for operation of high case–picking requirements. The extremely flexible load-handling device reduces manual handling and allows for high performant manual goods-to-person or fully automatic case picking.
Storage Solutions for Container, Bin and Carton Loads – Scalable solutions using Miniload cranes or storage shuttle systems that are capable of handling loads of varying dimensions. Multiple deep storage capability maximizes storage density whilst the selection of Miniload, Flexi Shuttle or Cuby aim to optimize the final solution according to different load and performance requirements.
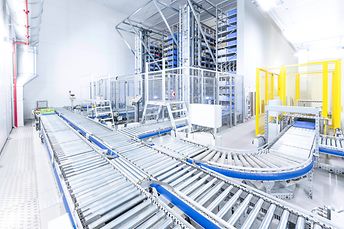
The material flow process from storage and retrieval, picking and handling of the SKUs (Stock Keeping Units), the journey needs to be carefully designed to prevent unnecessary conciliatory between storage type and location, picking, packing and shipment, and the nature of the goods. There are concepts important to adopt to minimize the time of these operations and performing them correctly, which can create more efficiency in even the most complex operation.
Warehouse Management & Monitoring Abilities
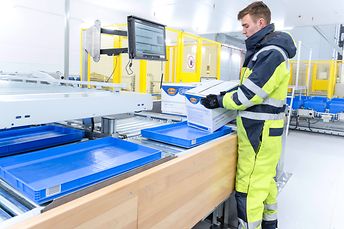
Clear visualizations and comprehensive tools that manage processes, resources, and stock levels facilitate the set-up of an efficient warehouse operation. Although there are a wide mix of warehouse automation technologies that would keep track of inbound and outbound goods is important, issues such as coordinating multiple systems often arise and the role of software looms larger. But what kind of security and surveillance capabilities does a software need to have?
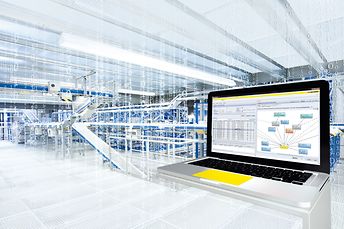
Tailored solutions for all requirements, SSI SCHAEFER develops and implements scalable, energy efficient systems for all conditions. All the above systems can be controlled via the WAMAS® or SAP EWM (Extended Warehouse Management) logistics software, from mobile racks right through to multi-aisle high bay warehouses with storage-retrieval machines, shuttle solutions and conveying systems. This all comes from one source and can even be made into a turn-key solution for warehouse renovations or construction of new warehouses with built-in fire prevention, for instance, sprinkler concepts or oxygen reduction.
With SSI SCHAEFER’s deep-freeze and temperature-controlled logistics, all legal obligations are implemented as standard. This includes HACCP hygiene standards, BBD guidelines, and the required traceability.
Optimum Solution Finding
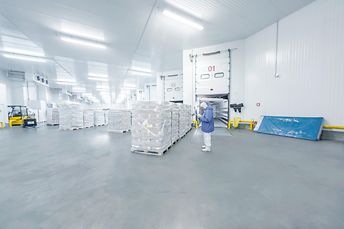
Future-proof logistics solutions need to seamlessly blend in with your individual processes. They must be infinitely variable and able to flexibly adapt to new framework conditions. You need specialists for this. You need experts who do not just focus on individual systems and services, but on full solutions.
In the context of cold-store solutions this will also include, but not be limited to external systems such as:
• Using airlocks between different temperature zones
• Separate labor-intensive working areas, place them into non-freezing environment
• Limited product exposure in non-chilled areas
• Customizing the rack design to the desire needs and space saving
• Making use of data analysis and simulation to produce the most efficient material flow design
• and many more…
A diverse spectrum of social and technological developments will shape your warehouse and logistics operations. If you have questions about introducing semi-automated or a fully automated process into your warehouse, contact us for a free consultation to kick start your warehouse transformation journey.
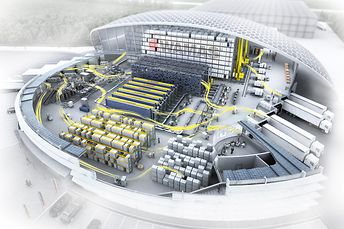
Disclaimer:
This article was originally published in the July 2023 Issue of Global Supply Chain’s magazine. Read the full interview here (page 28 – page 31) here.