Pallet Racking 101
Easily the most widely used storage equipment in the industrial world, pallet racking system can be found in most warehouses and manufacturing facilities. By stacking up pallets in an organized and efficient manner, it ensures goods stored within the warehouse are readily accessible.
Many options are available to meet different requirements, from the entry level Selective Pallet Racking to Drive-In, Channel storage, Push Back and Pallet Flow. For the uninitiated, this can be all rather confusing. Which type of system should you install for your warehouse?
The short answer is: It depends. Here are some factors you should consider before making your decision:
Budget
Desired storage density
Floor space and ceiling height
Inventory accessibility
Inventory rotation
Load size and weight
Items stored
Product shelf life
Having determined your requirements, let’s take a quick look at the common types of pallet storage available.
Selective Racking
The most common system found in warehouses and DCs, Selective Racking provides 100% accessibility to every pallet. It is the least expensive option and can be used in a number of aisle configurations and paired with most lift trucks.
It is suitable for fast moving products in a busy warehouse. The main drawback is low storage density as numerous aisles are needed.
Push Back Racking
For higher storage density, you may consider Push Back Racking system. Through eliminating the number of aisles, it increases the storage capacity by up to 90% as compared with a Selective Racking System. it increases the storage capacity by up to 90% as compared with a Selective Racking System.
It works by placing pallet loads on a series of nested carts riding on inclined rails. As a pallet is loaded from the front, it pushes the pallet behind by one position. The reverse happens when unloading. When the front pallet is removed, the rear pallets automatically move forward to the front picking position.
In this last in first out (LIFO) system, you can store products 2-5 pallets deep through a single pallet position thereby increasing storage density. However, selectivity is sacrificed.
It has been installed in a variety of industries, from manufacturing to third party logistics. If you have a high number of products with more than 2 pallets per SKU, push back is an option you may want to consider.
Gravity Flow Racking
Gravity Flow Racking uses inclined roller beds creating dynamic storage system. Pallets are carried by gravity from the rear of the system to the front, with speed reduction rollers to control the movement. As items are picked from the front and stocked from the rear, the system allows both activities to be performed simultaneously.
This first in first out (FIFO) system is ideal for operations where inventory has a limited shelf life such as food, fashion and pharmaceuticals, or in cold store operations.
Drive-In Racking
Drive-In pallet racking systems are cost-effective solutions for high-density storage. Consisting of blocks undivided by aisles, they can be configured to store loads four or more deep, ensuring maximum storage within limited space.
With limited selectivity, the systems work best for homogeneous products stored in large quantities offering first in last out (FILO) operation.
Channel Storage
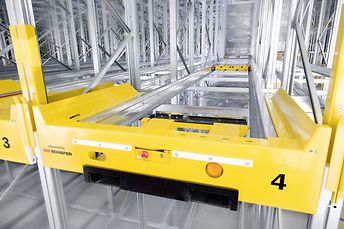
The channel storage system is ideal for high-density storage of largely homogenous pallets. With the help of the electric robot (SSI Orbiter), which runs on a track below the pallet, pallets can be moved within the warehouse safely and efficiently. With choices of either FIFO or FILO, it is a better alternative to Drive-In Racking Systems for facilities as pallet operations are far faster, and safer, with channels up to 25 deep space savings of between 15-20% can be achieved. Suitable for both ambient or cold store operations.
Mobile Pallet Racking
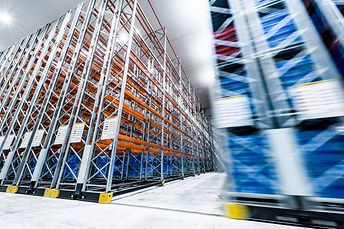
Mobile Pallet Racking can increase storage capacity by over 100% over the conventional static racks without loss of selectivity. Basically, the system consists of banks of Selective Pallet Racking mounted on an electrically driven mobile base, set on tracks embedded into concrete floor. By limiting the number of service aisles, as each bank can have between four to eight moveable racks, the system can slash the required storage footprint by as much as half.
The system, which can be built up 12m+ meters fully utilizes available height, it is ideal for high-cost warehouse operations such as cold stores maximizing the storage capacity.
Very Narrow Aisle (VNA) Racking
A variant of Selective Pallet Racking, the VNA provides higher density with 100% selectivity. By reducing the aisle space to marginally wider than the load, and raising the rack height to optimize the vertical space for pallet storage, it helps companies to maximize their warehouse capacity.
VNA racking of up to 17 meters is possible with advancement in forklift trucks which can operate in tight aisles. Pallets are stored and retrieved using special side loading fork truck able to manoeuvre in a narrow aisle of about 1800mm.
Automated Storage and Retrieval System (ASRS)
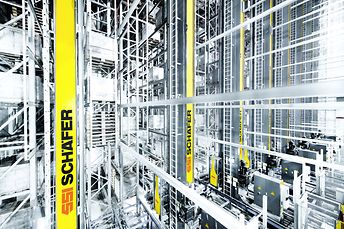
For fast and efficient pallet storage and retrieval nothing beats the ASRS. Operating at high speed, it ensures timely inventory supply for both order-picking and manufacturing operations. The computer controlled system offers real time and accurate inventory visibility eliminating the need for physical inventory inspections.
Using a computer driven crane systems can now be built over 40m high, similar to conventional racking systems, double deep and multi deep channel systems can offered.