Small Parts Storage Made Easy
Storing small parts or products can be challenging, especially when the number of SKUs a company has to store run into the thousands. Thankfully, a comprehensive range of shelving systems supported by software is now available to meet different requirements and price points to help companies store and organise small parts for easy retrieval.
Manual systems
Flexible and scalable, the manual small parts shelving is a good entry level shelving system. It is available in different configurations – single-tier, multi-tier, mobile and carton flow.
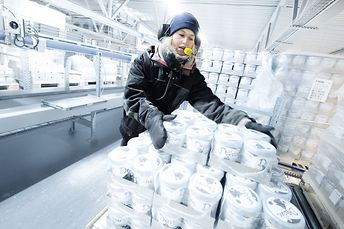
With the use of technology, you can increase productivity, improve efficiency and optimise the available manpower. Barcodes and RFID can bring about a quantum leap in inventory control and materials tracking, while pick-by-light, pick-by-voice and RF guided picking can increase the pick up as well as reduce error rates. Pick-by-light speeds up the pick process by directing the operator’s attention to the requisite pickface by light, while pick-by-voice frees the operator’s hands to concentrate on order picking, both resulting in increased pick quality and speed.
Semi-automatic system
For higher density storage and retrieval of slow moving parts at average pick rates like spare parts, for example, Vertical Lift Storage is a good option. Resembling an oversized drawer cabinet, it operates at the touch of a button, delivering trays with stored items to the access window. Being modular, it can be easily integrated into any existing system and can be locked when not in use. At about 120 picks per hour, it is a system tailor-made for slow movers. Let’s take a look at some of its key features by downloading the Vertical Lift Modules whitepaper here.
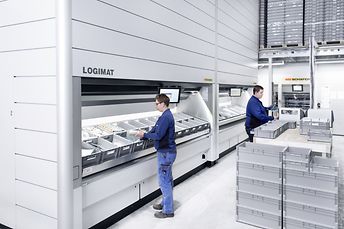
For high pick rates of slow-moving parts in e-commerce, pharmaceutical, retail and similar operations, goods-to-person (GTP) provides a combination of automated storage with manual, yet stationary picking operation, achieving rates of more than 1,000 picks per hour. Depending on storage volumes and pick rate such ergonomically optimised GTP stations may be supported by Miniload, horizontal carousel or shuttle operated Automated Storage and Retrieval Systems (ASRS).
Fully automatic systems
For fast, efficient operation with good accuracy, nothing beats the fully automated systems. Several storage systems are available, each with its plus points. The choice of what is appropriate depends on the type of operation you are in, the daily volume, turnover rate and pick rate. Among the options available are:
Robotic Picking in combination with Miniload, carousel or shuttle Automated Storage and Retrieval System: If you have a large number of SKUs, the right selection of Automated Storage and Retrieval system is a good option for your operation. It can house large number of SKUs in trays, cartons or totes and supports automatic replenishment to pick-by-light operations as well as goods-to-person and robotic picking.
A-Frame automatic dispenser: If speed is what you need, it is difficult to beat the A-Frame. Consisting of dispensers in two rows configured in the shape of an A-frame, it distributes products at high speed from vertical channels into totes, boxes, containers or conveyor belt travelling through the centre of the material handling system. The top of the range model can fulfil over 1,700 orders with a total of more than 40,000 order lines per hour. The A-Frame is ideal for products with uniform profile, like cosmetics, pharmaceuticals and stationary.
In a typical Pareto distribution system of slow, medium and fast-moving SKU, quite often a combination of storage and picking systems is needed within a facility to complement each other. For instance, you may have the A-Frame for the fast-moving SKUs, an automatic storage and retrieval system for the medium speed and possibly a manual shelving area for really slow moving items.
To make an informed decision, do check out with a competent consultant who can assist you.