Overcoming Space Constraints
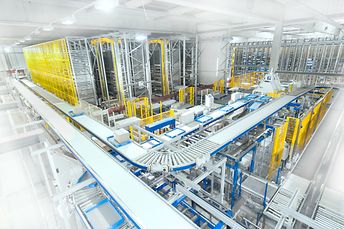
Gone are the days when warehouses are cavernous buildings in obscure locations of interest only to people who work in them. Today warehouses are hot attracting the attention of many, from young entrepreneurs to industrial property giants.
Thanks to e-commerce demand for warehouse space has reached new levels. With the proliferation of smart phones and tablets, e-commerce sales even in mature markets like Japan are enjoying double-digit gains.
Commercial real estate services agency Colliers International expects supply will not be able to keep pace with demand at least for the next five years at current construction rate.
If your interest is only in warehouse real-estate, it is a good time to make some extra bucks and well located warehouses are changing hands at top dollars. But for the operational man, it throws up some issues. For starters, how can you squeeze more space within your existing distribution centre (DC) to accommodate this demand surge?
Allow me to offer some suggestions:
Optimising available space
Take a critical look at your DC. Are you making optimal use of the existing space?
The vacant space above your warehouse floor is a storage expansion opportunity. Space can usually be found above cross aisles, above work and pick areas and even within the storage cube. Ceiling height – you can take full advantage of it. Floor space is finite, but vertical storage can increase the amount of products you can store.
Installing appropriate storage systems
Storage systems – are they helping you to maximize your space?
One of the fastest ways to create space within the DC is to add a mezzanine or raised storage platforms. One, two or even three levels high, it allows you to change empty overhead space into usable storage areas. They can also be used for work functions such as packaging or shipping preparation.
For facilities with ceiling height, there is a range of storage systems facilities you can consider, each with its merits and price points.
For pallets, the options include Very Narrow Aisle Pallet Rack (VNA) which can extend up to more than 17 metres high or high density racks with automated storage and retrieval system, where advancement in crane technology has enabled racks to extend up to 45 metres high.
For small parts storage, vertical lifts which can stretch up to 20 metres high is recommended. Being modular, the systems can also be integrated into any existing system and relocated with equal ease.
Investing in automation
Incorporating some level of automation in warehouse operation invariably raises warehouse efficiency. It doesn’t even have to be expensive.
Using barcodes and RFID for instance can bring about a quantum leap in inventory control and materials tracking.
By installing conveyors for receiving and despatch, you can increase productivity and reduce transport turnaround times. Equally conveyors can be integrated into order picking systems to improve productivity and expedite throughput.
Warehouse redesign
But you may want to take a step further – to redesign the warehouse interior and equip it for an Internet age. It is an option worth considering if your DC belongs to a different generation and it is out of sync in today’s multi-channel world, where purchases can be made from a store, website, interactive television or mail order.
In the past, DCs could store all units of a particular item in a single picking location in pallet-size quantities. But today, they will need to have multiple distinct storage locations for each item to facilitate picking in pallet, case or single item to meet the requirements of the different sales channels.
While warehouse redesign may sound costly, it is an investment that should pay for itself in a short period of time. If you are uncertain what option to take, contact a competent consultant who can assist you.