Obsolescence Management: Always one Step Ahead
Wear and tear, defects and even discontinuations can pose a real risk for system operators – in the worst-case scenario, they can even lead to a shutdown. To prevent this, proactive action is required. The solution? Obsolescence management: Through strategic planning and implementation of necessary measures, failures can be avoided, costs reduced and the lifecycle of machines efficiently extended.
What is obsolescence?
The term obsolescence comes from the Latin word “obsolescere”, which means “to become obsolete” or “to wear out”. And that's exactly what it's all about: Items, products or even software that no longer meet the latest standards and are therefore no longer produced or supported. Even at SSI SCHAEFER, some older items are occasionally discontinued – this is the only way to offer the best, state-of-the art solutions. Obsolescence cannot be prevented, but it can be managed.
Why obsolescence management is so important
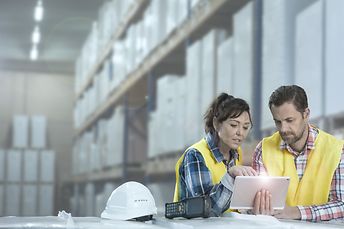
Proactively addressing obsolescence is therefore a part of risk management. It ensures maximum availability, better performance and optimal planning security – all crucial factors for the successful operation of a complex logistics system. By preemptively replacing discontinued components, repair costs can also be saved and the lifespan of the machines can be significantly extended.
Obsolescence management is a secure, cost-efficient and sustainable way to manage the product lifecycle of all of the parts of a system. But what does it look like in practice?
The 3 pillars of obsolescence management
Obsolescence affects individual items and wear parts as well as more complex products and software solutions. However, they all have one thing in common: When a discontinuation is imminent, action must be taken as early as possible. Depending on the application, three different options are available: A direct replacement, a last order or a complete retrofit.
Direct replacement
Suppose the discontinued item is merely a simple scanner. In most cases, it can be replaced 1:1 by another. If a small adjustment such as an additional cable is required, it is referred to as an “almost 1:1 replacement”.Last order
If no direct replacement for an item is available, customers receive a kind of advance warning – and the opportunity to order it one last time before discontinuation. This way, they gain valuable time to define a suitable retrofit for the affected machine.Retrofit
If no direct replacement is possible upon discontinuation, a retrofit provides a solution: With a so-called retrofit, an old machine can be upgraded to be state-of-the-art. The extent of this upgrade can vary significantly.
What is important in obsolescence management?
For successful obsolescence management, comprehensive documentation is essential. Only when all information on every single item is available can efficient long-term management be ensured and failures prevented. At SSI SCHAEFER, this involves using not only our own data and that of our suppliers, but also an additional service provider for lifecycle data.
Staying up to date
The best data is useless if it is not reliably communicated. As soon as it is clear that an item has reached the end of its lifecycle, SSI SCHAEFER customers are the first to know: A dedicated team of specialists at SSI SCHAEFER takes care of obsolescence management and proactively provides all necessary information.
Optimum overview
The larger the system, the more complex the obsolescence management. It is advisable to have all data transparently available in one place. At SSI SCHAEFER, this is possible through the online store: Here, the status of all components can be checked at any time and available spare parts can be ordered directly online. If a retrofit is necessary, all information, including indicative prices, is available for download.
If a detailed lifecycle report is used, potential discontinuations and the general condition of a system can be best assessed. SSI SCHAEFER also offers this service through the online store.
About the authors:
Steffen Seipelt
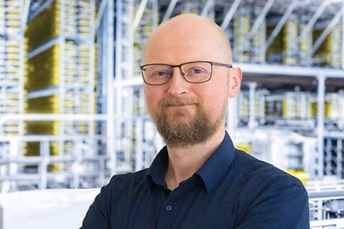
Alexander Süß
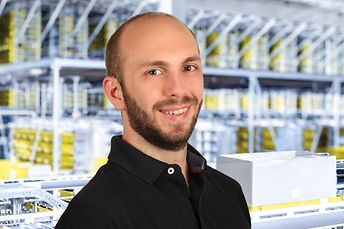