Joining in the Fight against Fake Medicine
The pharmaceutical industry is subjected to a web of rules and regulations governing the patenting, testing, safety, efficacy and marketing of medicines. Keeping track of the developments can be a challenge.
The rise of counterfeits is adding another dimension to the challenges the industry faces. As counterfeits endanger lives by containing incorrect or no active ingredients, governments have phased in regulations to combat fakes, which the World Health Organization estimates account for over 10% of medicine sales. Some countries require companies to track production by batches, manufacturing dates or even individual doses.
The US and EU are at the forefront in the fight against fakes. Over the next few years they are bringing in requirements on serialization and traceability. Under the EU’s Falsified Medicines Directive for instance, every pack of medical prescription has to be marked with unique identifier, which allows not only for identification but authentication. Each serial number also has to be registered with a pan European database, allowing pharmacies, hospitals and potential consumers to authenticate it. The 2D matrix barcoding which includes a 20-character alphanumeric serial number, product code, batch number and expiry date is the technology of choice for governments.
Creating a supply chain that is visible end to end is presenting huge technical challenges for the industry. Companies are investing large sums of money to develop and implement systems to facilitate the massive flow of data from generic manufacturers to contract packers, wholesale distributors, dispensers, pharmacies and clinics.
Why should it concern us?
Given the scale of the problem, governments will be forced to act lest it undermines the credibility of the healthcare system. And in our globalised world, whatever happens in the EU does not stay there. All companies that produce prescription medicines for the European market, including generic manufacturers, contract packers, re-packers and companies that import prescription medicines into the EU must subscribe to the directive.
Equipping DCs
Having automated systems is a distinct advantage in enabling pharmaceutical DC in meeting compliance: It is reasonably easy to install features to facilitate real time tracking of the entire process – from receiving, quality control, putaway, replenishment, counting, to pick, pack, and ship operations. The data can be formatted to record item, lot and warehouse history, as well as detailed date, time and user information, and stored electronically. The system can also provide automatic alerts of exceptions – when items don’t match batch tickets for example.
The manual DCs found commonly in pharmaceutical DCs in Asia will have to scale up before they can meet stiffer demands on traceability.
What kind of automated systems are best suited for pharma?
For order picking, you can count on the A-Frame and the carousel system. With the Schaefer A-Frame for instance, companies can easily achieve order picks of over 1,000 orders per hour, each with 20 or more different items. Its carousel system provides high pick rates of 1,000 picks per hour as well as high storage density.
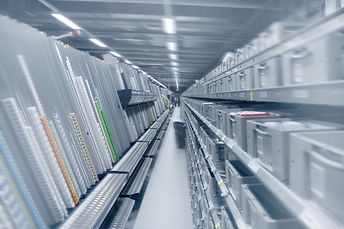
For error-free orders, nothing beats the automated order verifier which ensures virtually zero error rates. Used as a stand-alone solution or as an add-on to existing facilities, it also enables order traceability and authentication, facilitating compliance to legal regulations.
To learn more about these automated systems and how they can help to improve your DC, contact us for more information.