Getting to Grips with Order Fulfilment in Online Retail
However you choose to look at it, the online retail market is big and getting bigger. Whether you are in US, Europe or Asia, annual online retail sales are in the billions, and growth is in double digits. According to a recent Forrester Research forecast sales in Asia’s top five online retail markets – China, Japan, South Korea, India and Australia – could more than double in five years to US$858 billion in 2018.
With such eye-popping numbers, even retailers whose bread-and-butter comes from brick-and-mortar are looking at how to leverage on the Internet and win.
In the battle for eyeballs, having a stand out website which can differentiate it from the competition is a necessary prerequisite. Challenging though this can be, what comes next may be equally difficult. How do you fulfil these orders and deliver them to the customers within the time frame they expect?
Online order traits
Certain characteristics of online orders have made the task of order fulfilment problematic. Among them are,
Many small orders: Online orders are usually small and picking small orders is generally less efficient than picking large orders;
High number of SKUs. While having a wide range of products helps to drive traffic through the channel, it also slows down order picking at distribution centres (DCs);
High percentage of returns: Laxreturn policies may have given online retailing a huge boost, but it is a bane for DCs. The receipt, identification, evaluation, sorting, repacking, restocking and crediting of returns can be both labour and space intensive;
Special packing requirements: As online orders are typically small, they are often despatched in post packs, satchels or small cartons, which require a separate packing facility; and
Fast response time requirements: Speed of delivery is key as anyone who can place orders at a click is not likely to have the patience of Job.
Dealing with challenges effectively
Batch picking is the simplest way to overcome the inefficiencies of small order picking. While most modern Warehouse Management Systems have the functionality for batching orders, there are still many factors to consider in determining the optimal batching strategy.
Batching by SKU ensures high pick efficiency, as each SKU location is visited only once. The larger the batch, the bigger is the gain in picking efficiency. The downside of this is the cost of sorting the items into individual orders.
Multiple orders can also be batched together for picking. Sortation is easier than batching by SKU but picking efficiency is not as high, as each location is visited more than once.
Irrespective of what your preference may be, single item orders, which account for a high percentage of online businesses, should be batch picked into plastic tote bins. Since they require no sortation, they can be sent immediately for packing and despatch.
What is the appropriate size you may ask? The more orders in the batch, the greater is the increase in picking efficiency. Ideally, a full day’s orders are batched together so that a pick location is only visited once a day.
This may not always be possible. Order cut-off and despatch times may well be part of an online business’ value proposition, and orders received by say 11am have to be despatched the same day. The batch size is also limited by sort destinations availability. If there are 2,000 orders a day and only 200 sort destinations then 10 batches are required.
Arriving at the optimal batch size requires an understanding of the issues involved and some mathematical modelling.
Other options
Cluster picking is another option you can consider. A number of containers are put on the trolley, each representing a separate order. The more orders you have on a trolley, the better the picking efficiency.
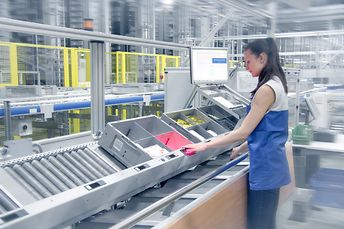
Conveyor based picking is ideal for fast moving or promotional items. Empty order totes can be relayed to operators by conveyors. Once the orders are filled with the requisite items from carton live storage or pallets, the totes can be carried away to the next picking zone. This reduces operator movement and raises efficiency.
Goods-to-Person (GTP) is fast, efficient and accurate but it may not be suitable for all items based on return on investment (ROI).
Automatic sortation
While batching makes sense for online businesses, the items picked have to be sorted to individual orders. What is the optimal way of approaching this?
One of the most efficient ways is to use a unit sorter which can automatically sort individual items to different chutes. There is a range of unit sorters in the market with varying throughput and product handling characteristics. Major considerations for automated sorters are throughput in items per hour and the number of chutes.
Ideally, to maximise picking efficiency, there should only be one batch picking per day. But this is not possible with sizeable lots. For 1,000 orders per day, you need a sorter with 1,000 chutes, which is just not feasible. By breaking the daily orders into 10 batches of 100 orders each, you require only 100 sort destinations.
Reducing the number of touches
While batch picking and sorting of orders increase picking productivity, they also increase the number of ‘touches’ into the process:
Touch 1 – Batch picking items by SKU into totes (for transport to a sorter induct)
Touch 2 – Taking picked items from totes and placing them on the sorter induct (for automatic sortation to groups of orders)
Touch 3 – Taking sorted groups of orders and slotting them to individual orders at a put wall (or pigeon holes for manual sorting to order)
Touch 4 – Taking individual orders from the put wall and placing them into totes for transport to packing
Touch 5 – Taking individual orders from totes and packing them for despatch.
An effective way of reducing the number of touches and investment on equipment is to batch items by order. A number of whole orders are picked to the same tote, which is then transported directly to a packing bench fitted with a small put wall for sorting into individual orders. The packing operator can sort the items to order and repack them without moving from the packing bench. A sorter is not required and the number of touches can be reduced, which can mean a better overall ROI.
A range of automation options is available to help companies to improve productivity and accuracy in fulfilling online orders. Finding the right combination between automation and flexibility requires a detailed analysis of the profile of the online orders and SKUs, including a clear understanding of all key drivers and constraints. To make an informed decision, do check out with a competent consultant who can assist you.
Source origin from Brad Welsman, Managing Director of SSI SCHAEFER Australia.