From Man to Goods to Goods to Man
After much hesitation, companies in Asia are beginning to adopt automation in the warehouses. While some automation in the warehouse to improve the order pickers’ lot may seem like a no brainer, as order picking is time-consuming, Asian operators have preferred to rely on manpower. In the past, it was easy to fill warehouse with low cost foreign labour where their numbers could be increased during the peak seasons and reduced during lull periods.
We are seeing a perceptible shift in some countries. In Australia, Hong Kong, Korea and Singapore, where the cost of labour and the availability of labour are key concerns, existing warehouses are being retrofitted for improved efficiency. Even in Indonesia – a young nation of over 250 million people – we are seeing a greater requirement for automation. With hourly minimum wage of US$0.56 (as against US$17.40 in Australia), cost is less of an issue but geared to speed and accuracy of picks.
Changing demand is forcing the pace. With growing affluence, convenience stores like 7-Eleven and FamilyMart are springing up across the region.
These stores with a footprint of 200-500m2 can carry between 2000-3000 skus with no buffer storage, so replenishment is daily, they are serviced by a central Distribution Centre, with one Distribution Centre serving up to 1500 stores. With such a high level of daily piece picking, some intelligence to the warehousing operation is essential.
As the car population expands across the region, auto parts suppliers are pushed to automate to handle the many part numbers quickly and accurately.
By making a shift from a manual operation – man to goods – to goods to man, companies can expect to enjoy a quantum leap in their productivity. Studies have shown that walking, searching and selecting can take 75% of an order picker’s time. By eliminating all three, you can raise productivity by a factor of four.
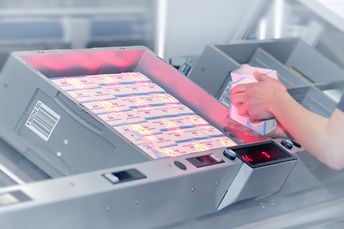
An order picker walking around the warehouse looking for picks can do 60 to 80 picks an hour. If you can reduce walking by installing conveyors for instance, the pick rate can increase to 300 picks per hour. With goods to man picking, the pick rate can easily go up to 1,000 pick rates per hr.
Preferred options
What are companies’ preferred options? Much depends on the nature of their operation. An auto parts supplier in India has gone for the ASRS and Goods to person picking (GTP), in order to cope with the complexity of high number of Sku’s and picking numbers. With the spike in car population with growing affluence, this trend is now being considered by other automotive companies. A more cost-effective alternative solution is Kombi Logistic Solutions (KLS), where a combination of standard shelving solutions with conveying systems can bring some intelligence to the warehouse with a lower investment.
Carton flow racks – these gravity flow live storage systems help to expedite order picking
Conveying system – an indispensable conduit in the order fulfilment system
R3000 offers a modular off-the-shelf system, companies can retrofit their existing warehouses, with multi-tier shelving
Palletise systems using high-density storage, or high rise racking systems can reduce floor footprint