Solve the Top 3 Problems in Cold Storage Logistics
The current crises have caused many industries to evaluate operations because they highlight and even aggravate known problems. For instance, lack of digitization or the shortage of skilled workers have exposed a somewhat fragile ecosystem. Solutions to these challenges are needed quickly to remain competitive and secure the future of many companies. Cold storage logistics is one of the sectors that calls for new solutions.
For this reason, the operators of freezer warehouses were forced to find new solutions. Continuing status quo is not an option. To reduce energy costs, counteract the shortage of skilled workers, and efficiently manage space requirements for future growth, companies should consider semi- or full automation for warehouse storage or distribution fulfillment. Regardless of whether it is about expanding an existing system or building a new distribution center, SSI SCHAEFER offers future-oriented storage solutions for cold logistics. In addition, each system is custom to meet the needs of individual customers.
In our Best Practice Guide on cold storage logistics, you will find all relevant strategies for future-proof frozen storage warehouses.
Automation to solve problems for frozen storage warehouses
Automation is a proven and future-proof way to solve three major problems of cold storage logistics:
Shortage of skilled workers
Lack of space
High energy costs
Minimize manual activities in cold storage warehouses
The shortage of a qualified workforce is one of the most common problems today. Working in a warehouse often involves lifting heavy loads, repetitive tasks, and also working at dangerous heights. The shortage of skilled workers is particularly an issue in cold storage warehouses. Working conditions in these areas are generally less attractive to employees because they have to spend part of their working day in very low temperatures.
This becomes even more apparent when it comes to manual tasks. For example, employees who are responsible for picking and forklift drivers who spend a large part of their working day inside cold storage facilities.
While automated systems will save on labor, it’s meant to speed up throughput, increase storage density and to limit exposure to harsh conditions.
Another possible solution is to rework material handling processes with adding in certain elements of automation. Conveying systems, shuttle storage areas or storage-retrieval machines can be used for handling, storage and picking of bin and pallets, as well as the subsequent transport of the load carriers to the workstations. With this type of solution, employees are involved in order picking at ergonomic goods-to-person workstations and in an environment that is above freezing. The working conditions become more attractive to potential employees.
High density storage for freezer warehouses
Space limitations is one of the three main reasons for companies to extend existing systems or commission an intralogistics expert to check the layout of the current premises, integrate new solutions into the existing system, or switch to semi- or full automation.
Cold storage warehousing requires simple and fast handling. If semi automation is currently the better solution, mobile racks are an option. These racks optimize space requirements and provide high storage capacity. Space in deep-freeze warehouses is expensive, so a technology that creates additional storage area with minimum aisle space should be implemented.
One can also optimize space with a fully automatic solution, such as a high bay warehouse (HBW). It makes optimal use of the entire vertical space. The HBW is a fully automatic rack system in combination with storage-retrieval machines (SRM) for extremely intense storage on the smallest footprint. This is particularly important in cold chain because each cubic meter in the warehouse must be adapted to specific conditions.
Quite often, an automated solution solves more than one problem. For instance, an HBW not only requires less space but also uses less energy thanks to the dense construction.
Optimizing energy use in cold chain logistics
Energy costs are one of the most important cost factors for companies utilizing cold chain operations. For manual storage, the racks must be adjusted in width so that products can be picked manually as well by forklifts. This means more space for cooling and lighting is required, and this increases the costs. However, optimizing energy costs by implementing automation is an excellent tool to support companies with lowering operating budgets and boosting profits.
For semi automation, channel storage systems are also a good solution. These systems offer a compact storage solution within a defined area. Several storage locations are arranged one after the other in so-called channels. A channel storage system is particularly consolidated and uses space more efficiently than common racks.
Fully automatic shuttle systems and pallet SRMs are built with energy savings in mind. Many solutions can even work in the dark or with less lighting for more sustainable benefits. This is something that cannot be achieved with manual processes.
Tailor-made solutions as a key to success for cold storage logistics
The above-mentioned solutions are examples of how companies can meet the challenges of cold chain logistics. Every solution should adapt to the existing business model and the current needs of the customer.
The perfect implementation for an organization will be based on a data analysis. It will include the available space, operating costs, and future goals. A reorganization with only internal resources may be challenging, and that’s when an intralogistics expert can assist. SSI SCHAEFER offers every company, independent of size, custom solutions that achieve well defined goals and success criteria.
The team of experts at SSI SCHAEFER can tap into many years of experience with some of the largest cooling systems worldwide, but our experts have also implemented many small and medium-sized solutions. Every solution is tailor-made to the specific business requirements of the customer.
What SSI SCHAEFER customers say
We could have kept the organization as it was 35 years ago – with completely manual operations. We were aware that we were no longer able to compete effectively. The only way to stay in the competition is to use technologies.
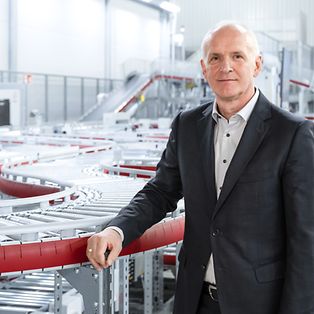
As the first provider of fully automatic deep-freeze solutions in the Philippines, ORCA is the one and only company to invest to that extend in food infrastructure. As a sales head, I saw how customers gravitated to our brand because of the promise of automation. We also experienced first-hand how the market perceives the value that innovation can bring.
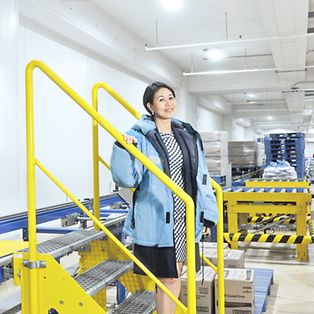
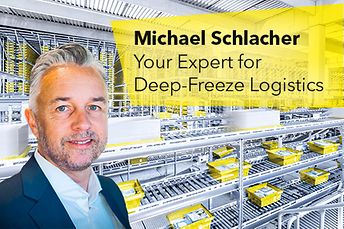
About the author:
After many years of experience in intralogistics companies, including senior positions in project management and sales, Michael Schlacher, joined SSI SCHAEFER in 2021 and is responsible as Senior Sales Manager, Business Development.